
- #Geometric constraints autodesk inventor pro 2015 pltw 5.2 code
- #Geometric constraints autodesk inventor pro 2015 pltw 5.2 series
A point coincident with a curve slides along the curve so that the point can lie anywhere along the curve, unless other constraint or dimensions prevent the point from moving.A point constrained to a curve can lie outside the extents of the curve.A coincident constraint is automatically created on the endpoints of curves created in succession with the Line command.When applying coincident constraints, keep in mind: Right-click and choose Done, press Esc, or select another tool or command.Click the geometry to which the point is constrained.In the graphics window, click to set the point to constrain.In an active sketch, click Sketch tab Constrain panel Coincident Constraint (2D)or 3D Sketch tab Constrain panel Coincident Constraint (3D sketch).The green coincident dot means the coincident constraints are enabled to remove in relax dragging in Relax Mode. Pause the cursor over a glyph to show the affected geometry. To identify the geometry affected by the constraint, hover over the yellow dot. The yellow coincident dot represents the presence of the constraint. In a 3D sketch, a coincident constraint can also cause points and lines to be constrained to surfaces. I am having difficulty with an assembly in terms of actually constraining the assembly.The Coincident constraint causes two points to be constrained together, or causes one point to lie on a curve.
#Geometric constraints autodesk inventor pro 2015 pltw 5.2 series
I have a series of linkages that are coupled so that I can drive the assembly with a pneumatic cylinder. However, the last constraint couples the cylinder with a Rod Clevis to tie it all together. I have tried to constrain the model with an insert constraint, but that did not work. So, I next tried to constrain the 2 items together axially with a MATE. This worked to line up the items with respect to the axis of each item, but I still require to constrain the items to set a position of the clevis on the shaft.
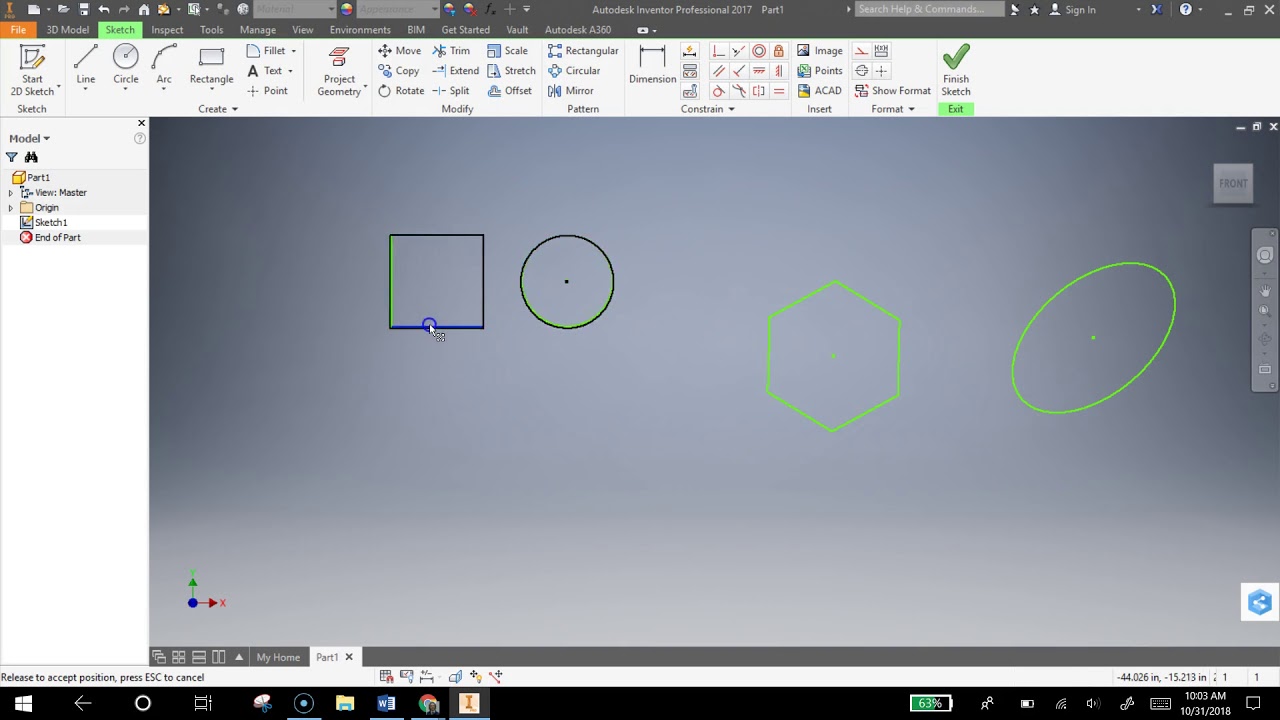
I know it is not an issue of the geometry not being able to actually accomplish this because I can manually move the 2 pieces through each other while constrained axially. RE: Drawing Constraints cadranger (Military) 3 Jun 03 08:35 Any ideas? Has anyone else experienced this issue with linkages? In dealing with linkages, the actual gemoetry will allow for 2 positions to be observed, and I wonder if this is why I am having such a time of it. I take it you want to fully constrain the assembly.

The problem is if we change the size of the door, the sketch lines don't stay in the corners, they just stay the exact size and orientation they were created.
#Geometric constraints autodesk inventor pro 2015 pltw 5.2 code
With any linkage, you should constrain the parts to actually allow them to move like they would in real life. Add Geometric Constraints in Drawing Document We have some code (attached DoorAnnotate.cs) that creates a door symbol as two sketch lines. Use the insert constraint for pins and bolts in the mating parts. You've used the mate contraint for axis (piston in cylinder for example). Linkages generally use rotational movement and linear movement in combinations. Once all the parts are linked and allowed to rotate and slide together, you should select the best constraint the will stop the movement. Sometimes its a mate or flush with offset between origin axis planes of two parts or just between two surfaces.

Using the angular constraint alone to do this is risky. Inventor doesn't respect angles very well. As you might see, the solution for a 10 degree angle can also be 180 degrees opposed. Inventor lets you state the angle but if the parts are closer to the 180 opposed solution it will use that. Once you find the ideal (there is always more than one solution)constraint, you can then use the "drive the constraint" tool. This allows you to set the links in motion with rotational and linear limits set by you so that the parts don't move through each other. You can check for interference between parts if you require a set movement but are unsure if the parts are actually touching. Good Luck RE: Drawing Constraints wendert (Mechanical) If you are still having trouble you can send me the assembly.

I had done as you have suggested to some degree. The difference being that The geometry of the assembly does not really lend itself to the final constraint that would disallow movement. The assembly is a series of linkages that don't really have a end or intermediate position that is easily defined. GEOMETRIC CONSTRAINTS AUTODESK INVENTOR PRO 2015 SERIES I built the assembly with both insert and mate constraints, but the final constraint that was to tie the assembly together would not take. GEOMETRIC CONSTRAINTS AUTODESK INVENTOR PRO 2015 SERIES.
